This comparison aims to provide insights into which type of geotextile is more suitable for specific applications based on factors such as strength, durability, permeability, filtration efficiency, cost-effectiveness, and environmental impact. By understanding the differences between woven geotextile and non-woven geotextiles, engineers and project managers can make informed decisions when selecting the appropriate geotextile for their projects.As the leading geosynthetics manufacturer and supplier, BPM Geotextile offer various types geotextile with custom thickness and size at best factory price.Let’s discuss it together – Ultimate Comparison Of Woven vs Non Woven Geotextile.
1. Woven VS Non Woven Geotextile – Basic Properties
1.1 Woven Geotextile
1.11 Structure
Woven geotextiles are created by weaving together synthetic filaments or yarns in a crisscross pattern, similar to how fabric is made. This weave can be tight or loose, depending on the application requirements.
1.12 Characteristics
- Tensile Strength: High tensile strength along the direction of the fibers due to the woven structure.
- Stiffness: More rigid and less flexible than non-woven geotextiles.
- Permeability: Generally lower permeability compared to non-woven geotextiles because of the tighter weave.
- Abrasion Resistance: Good resistance to surface abrasion due to the interlocking fibers.
- Tear Propagation: May have a higher tendency for tear propagation along the fibers.
- UV Resistance: Can be treated for UV resistance, but it varies depending on the material used.
1.2 Non Woven Geotextile
1.21 Structure
Non-woven geotextiles consist of synthetic fibers that are randomly oriented and bonded together using heat, chemicals, or mechanical entanglement without forming a weave.
1.22 Characteristics
- Tensile Strength: Provides uniform strength in all directions due to the random fiber layout.
- Flexibility: More flexible and adaptable to irregular surfaces than woven geotextiles.
- Permeability: Typically higher permeability due to the more open structure, making them suitable for drainage and filtration applications.
- Abrasion Resistance: Generally less abrasion-resistant than woven types, but can be improved with added layers or coatings.
- Tear Propagation: Better resistance to tear propagation due to the random fiber orientation.
- UV Resistance: Like woven geotextiles, non-woven types can be treated for UV resistance, and performance varies by material and manufacturing process.
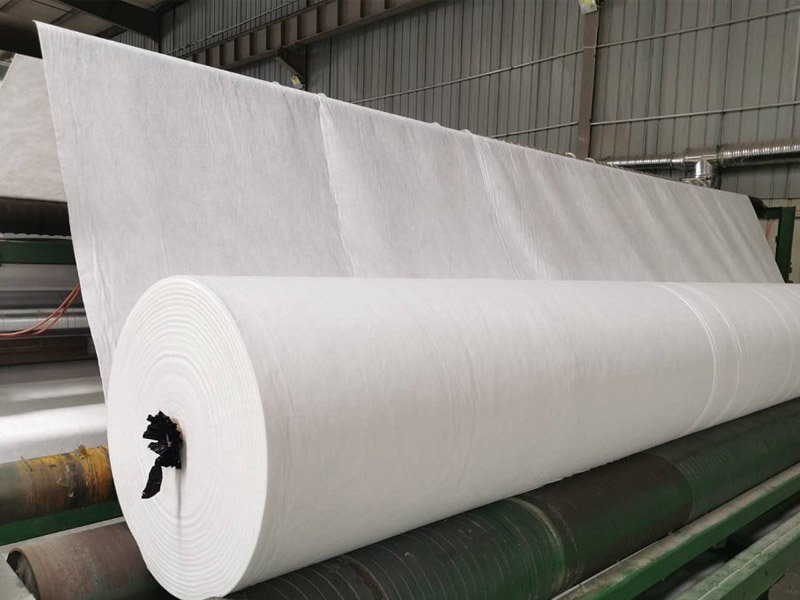
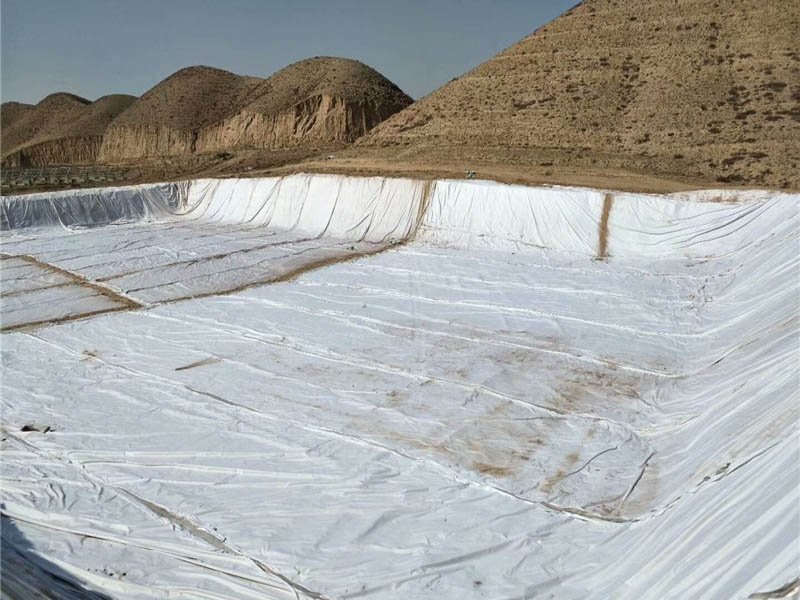
2. Woven VS Non Woven Geotextile – Typical Applications
2.1 Woven Geotextile Applications:
2.11 Reinforcement
Used in reinforced soil structures such as embankments, retaining walls, and slope stabilization to provide strengthening and increase stability.
2.12 Separation Layer
Acts as a barrier between different soil types to prevent intermixing, especially in road construction and railway beds.
2.13 Erosion Control
In coastal or riverbank protection projects, woven geotextiles can be used to control erosion and protect the soil surface.
2.14 Tunnel and Pipeline Protection
Used around tunnels and pipelines to provide a protective layer and prevent surrounding soil from collapsing into the structure.
2.15 Paving Sub-base
In roads and parking lots, woven geotextiles can be used under asphalt or concrete to reduce deformation and extend pavement life.
2.2 Non-Woven Geotextile Applications:
2.21 Filtration
In earthworks and civil engineering projects, non-woven geotextiles are commonly used for filtration to allow water to pass through while holding soil particles.
2.22 Drainage
Used in foundation drainage layers, leachate collection systems, and beneath capillary break layers to promote efficient water drainage.
2.23 Erosion Control
Commonly used for controlling surface erosion on slopes, embankments, and channels by providing a protective layer that stabilizes the soil surface.
2.24 Weed Barrier
Used in landscaping and gardening as a weed barrier fabric to inhibit weed growth while allowing water and air to permeate.
2.25 Root Barrier
Used to prevent the penetration of tree roots into drainage systems or other areas where root growth is undesirable.
3. Woven VS Non Woven Geotextile – Performance Comparison
3.1 Woven Geotextile Performance
3.11 Strength and Durability
Woven geotextiles provide high tensile strength and durability due to their interlocking fibers. This makes them ideal for heavy-duty uses like reinforcement and erosion control in stressful environments.
3.12 Permeability
Woven geotextiles have lower permeability due to their tight weave. This limits their use in filtration and drainage needs requiring high water flow.
3.13 Abrasion Resistance:
Woven geotextiles show good abrasion resistance due to tightly interlocked fibers. This benefit is important in applications with mechanical stress or movement.
3.14 Tear Strength
Woven geotextiles may tear more easily along the fiber direction due to their structure. This can be a concern in applications where damage is likely to occur.
3.15 Installation
The rigidity of woven geotextiles can make them more challenging to install on irregular surfaces or around curves, requiring careful handling to avoid damage.
3.2 Non-Woven Geotextile Performance
3.21 Strength and Durability
Non-woven geotextiles offer uniform strength in all directions thanks to their random fiber layout. They are versatile but may not match woven types’ tensile strength in high-stress situations.
3.22 Permeability
Non-woven geotextiles have higher permeability due to their open structure. This makes them suitable for filtration and drainage needs where water flow is important.
3.23 Abrasion Resistance
While generally less abrasion-resistant than woven types, non-woven geotextiles can be manufactured with added layers or coatings to improve this property.
3.24 Tear Strength
Non-woven geotextiles usually have better tear strength due to their random fiber arrangement. This helps prevent tear propagation and offers more resilience where damage may occur.
3.25 Installation:
The flexibility of non-woven geotextiles makes them easier to install on irregular surfaces and around curves, adapting well to different contours without damage.

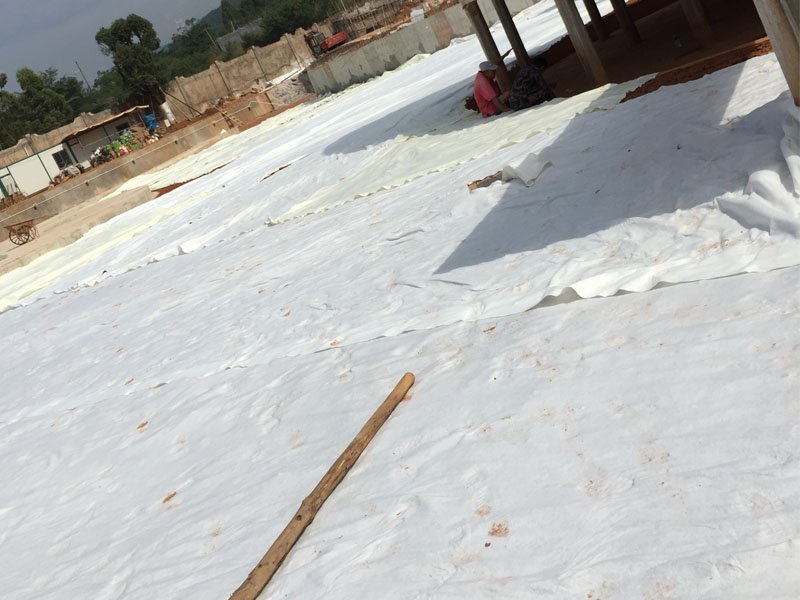
4. Woven VS Non Woven Geotextile – Cost And Lifespan
4.1 Woven Geotextile
4.11 Cost
Woven landscape fabrics cost more than non-woven types due to their complex manufacturing and high-quality materials. The price varies with the polymer type, like polypropylene or polyester. Extra treatments for UV resistance or permeability can also affect the cost.
4.12 Lifespan
Woven landscape fabrics usually last longer than non-woven types, with some lasting over 10 years. Their tight weave makes them durable and resistant to damage. This contributes to their longer lifespan.
4.2 Non Woven Geotextile
4.21 Cost
Non-woven landscape fabrics cost less than woven types due to their simpler production process. They are made by bonding fibers without weaving, making them more budget-friendly. This makes them a cost-effective choice for price-conscious projects.
4.22 Lifespan
Non-woven landscape fabrics typically last 2 to 5 years before needing replacement. Their fiber layout and bonding method may make them more prone to UV and wear damage. This results in a shorter lifespan compared to woven types.
5. Summary
The ultimate comparison of woven versus non-woven geotextiles hinges on their structural differences, which dictate their performance and suitability for various applications. Woven geotextiles excel in high tensile strength, durability, and resistance to mechanical wear but are costlier and less permeable, making them ideal for heavy-duty uses like reinforcement and erosion control. Conversely, non-woven geotextiles offer cost-effectiveness, higher permeability, and uniform strength suitable for filtration and drainage projects requiring effective water flow. The choice between the two should be guided by the specific needs, stresses, and budget of a given project.
If you have any questions or inquiries, please contact us, we will reply as soon as possible.